Different grain sizes are of different sandblasting and shot peening efficiencies. Selecting the proper grain size is important for both safety and cost control. When choosing the grain size, the following factors should be taken into consideration.
Factors to Be Considered
Adhesive Strength of Scale and Molding Sand
The finer the size of the steel shot, the smaller the impact load provided; and vice versa. The larger impact load of the large grain size steel shot results in prolonged blasting time, because of a less number of steel grains per weight. The first tip in selecting a steel shot, therefore, is to decide the proper size and hardness, in consideration of such adhesive strength of scale or molding sand.
Expected Surface Roughness
While fine steel shot provides a small impact load, a coarse one with a large impact load generates a rough surface and may end up with distortion, or at worse, bent of the subject being blasted. Such roughness is determined by the size of the steel shot and the differences in hardness between the steel shot and the subject being blasted. Therefore, the recommended size of the steel shot is determined based on the expected surface roughness and hardness of the subjects to be blasted.
Other Factors
Other than the two decisive factors described above, consideration should also be given to the size, material, and shape of the subjects to be blasted, and the operating conditions of the blasting machines.
For your best application, your work may be tested in your conditions at our laboratory and the optimum size of steel shot will be advised.
Size Distribution of Steel Shots and Steel Grits
The size distribution of steel shots and steel grits is as below:
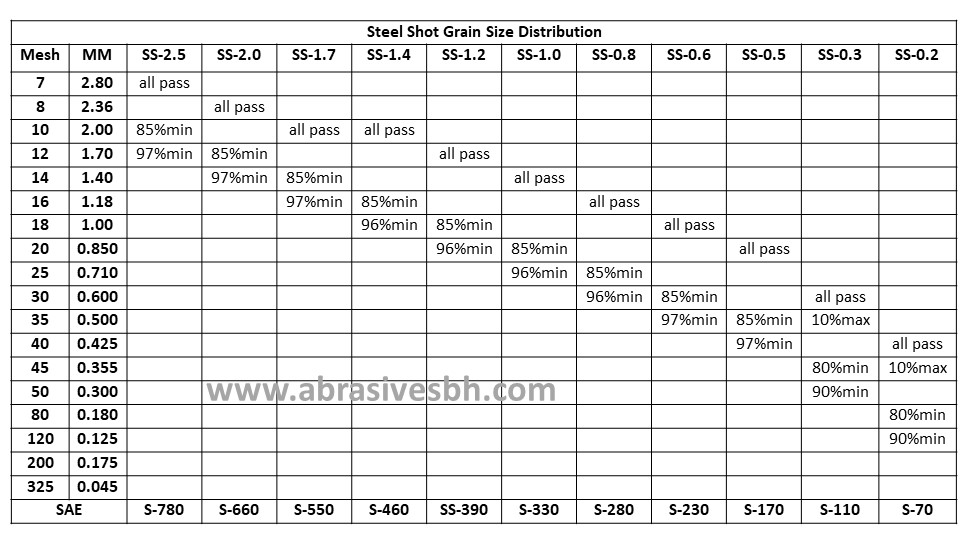

General Guidelines
Here are the general guidelines for your kind reference:
Steel Shot | Steel Grit | Applications |
S780 S660 | G10 G12 | Sand and rusts removing of large-sized cast iron, cast steel, steel structures, large-sized forging and surface treatment of oxidized workpieces. |
S550 S460 | G14 G16 | Sand-removing of large and medium sized castings, deoxidization of forgings, heat-treated pieces, steel plates, steel pipes, sections and steel structures, surface treatment before plating. |
S390 S330 | G18 G25 | Sand-removing of small and medium sized castings, rust-removing and intensification of forgings, heat-treated pieces, steel plates, steel pipes, sections and steel structures, surface treatment before plating, cutting of rocks. |
S280 S230 | G25 G40 | Sand-removing and deoxidization of small-sized castings, forgings, heat-treated pieces, aluminum-copper alloy castings, steel plates, steel pipes, sections and steel structures, surface intensification of springs and chains, cutting of rocks, grinding processing. |
S170 S110 | G50 G80 G120 | Sand-removing and rust-cleaning of alloy castings, thin plates, strip steel, and small-sized stainless steel castings, intensification of springs, surface treatment before plating, improving roughness, enhancing adhesiveness. |