Simple Introduction of Steel Shots
Steel shots are non-polluting steel blasting media used extensively in the blasting and cleaning industry to remove paint, rust, mill scale and other surface contaminants from steel, concrete and other surfaces prior to coating. Steel shot abrasives are also used to remove surface contaminations from castings after removal from the mould and also for shot peening operations on metal components which are exposed to severe stress in automobile and construction machinery industries.
In the application process, the steel shot blasting media is used almost exclusively in centrifugal wheel airless blasting equipment. The cost effectiveness is incomparable due to its impact resistance qualities, durability and with utmost cleaning capacity.
Summary of Production Methods of Steel Shots
There are three production methods of steel shots: Air Injection method, Water Jet Impact method, and Centrifugal Atomization method.
The centrifugal atomization process was originally developed by Pratt& Whitney Aircraft Manufacturing Company. Due to its unique grain size distribution, grain shape, cleanliness and cost-effectiveness, people pay more attention to it. Now it is the main method for producing cast steel shot in the industry.
Details of Centrifugal Atomization Method
Let us talk about the centrifugal atomization in this article.
The centrifugal atomization method uses centrifugal force to separate molten steel. The molten liquid is thrown out of a series of small holes at the edge of the rotary wheels and falls into the cooling medium, and cure to shape. Then the semi-products follow a series of thermal and mechanical treatments in order to attain martensite microstructure.
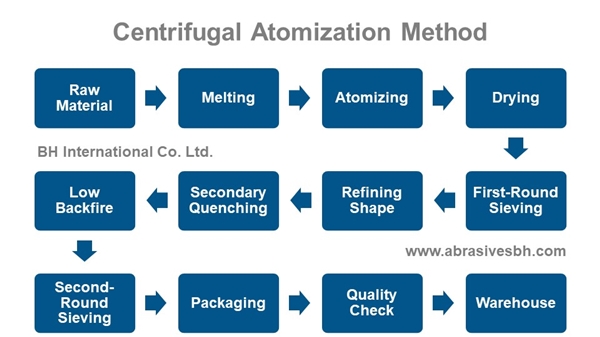
Detailed procedures are:
First step: raw material.
Steel scraps are the most widely used raw material. The steel scrap price the factor which mostly affect the steel shot market.
Second step: melting.
Steel scraps become steel liquid in this step.
Third step: atomizing.
The molten steel liquid is thrown out of the rotary wheel by centrifugal force and falls down into the cooling medium, and then steel shots are shaped.
Fourth step: drying.
Fifth step: first-round sieving.
The steel shots fall into rough categories according to their diameters, ready for the fine sieving later.
Sixth step: refining shape.
Roundness of the final product is determined by the refining machine.
Seventh step: secondary quenching.
Change the metallographic structure of steel shots and increase the hardness of steel abrasives.
Eighth step: low backfire.
Improve the toughness of steel shots and increase the durability of steel abrasives.
Ninth step: second-round sieving.
Steel shots will be strictly classified into specific grain sizes (from S70 to S780) after this step.
Tenth step: packaging.
Eleventh step: quality check.
Chemical composition (including C, Mn, Si, S, and P) and physical characteristics (including density, size distribution, structure and hardness) are tested in the typical quality inspection process.
Twelfth step: storage.
Keep the steel shot in cool and dry warehouse.
