
Shot peening is a widely used process to enhance the durability and fatigue resistance of metal components. This technique involves bombarding a surface with small particles under high pressure to induce compressive stress. Among the many materials used in shot peening, steel grit is one of the most common options. But can steel grit be used for shot peening effectively? In this article, we will explore the properties of steel grit, its role in shot peening, and whether it is the right choice for specific applications.
Steel grit is a popular choice for shot peening due to its high hardness and ability to create uniform compressive stress, which enhances the fatigue life of metal parts.
Understanding the various types of abrasive materials and their properties is essential for selecting the right one for shot peening. In the following sections, we will discuss whether steel grit stands out as the best choice, its advantages, limitations, and applications in shot peening processes.
Steel grit is an effective material for shot peening, but it may not be the best choice in every situation, depending on the material being treated and the desired outcome.
Table of Contents
What Is Steel Grit?
Steel grit is a type of abrasive material made from high-carbon steel that is produced through the process of crushing or granulating steel. It is commonly used for surface cleaning, shot blasting, and, more importantly, for shot peening due to its unique properties.
Steel grit is a high-carbon steel abrasive, ideal for shot peening due to its hardness and ability to create a consistent surface finish.

Steel grit has an angular shape, which helps create deeper indentations on the surface of materials, making it effective in generating compressive stress. The hardness of steel grit typically ranges from 50 to 60 HRC (Rockwell Hardness), which allows it to withstand repeated impacts without breaking down quickly. This durability makes it particularly useful in shot peening, where longevity and consistency are critical.
Steel grit, with its angular shape and high hardness, is a solid choice for shot peening when durability and effective surface compression are required.
How Does Steel Grit Compare to Other Materials for Shot Peening?
When it comes to shot peening, several abrasive materials can be used, including steel shot, ceramic beads, and glass beads. But how does steel grit stack up against these other options?
Compared to steel shot, steel grit is more angular and harder, providing greater surface indentation and creating stronger compressive stress.
Steel grit is known for its sharper, more angular particles, which help create deeper indentations and more compressive stress on the surface of the workpiece. In contrast, steel shot is spherical, which means it is less aggressive and better suited for applications that require a smoother surface. While ceramic beads are more brittle and tend to break down faster, steel grit holds its shape longer, making it more cost-effective for prolonged shot peening operations. However, the choice of material often depends on the specific requirements of the application.
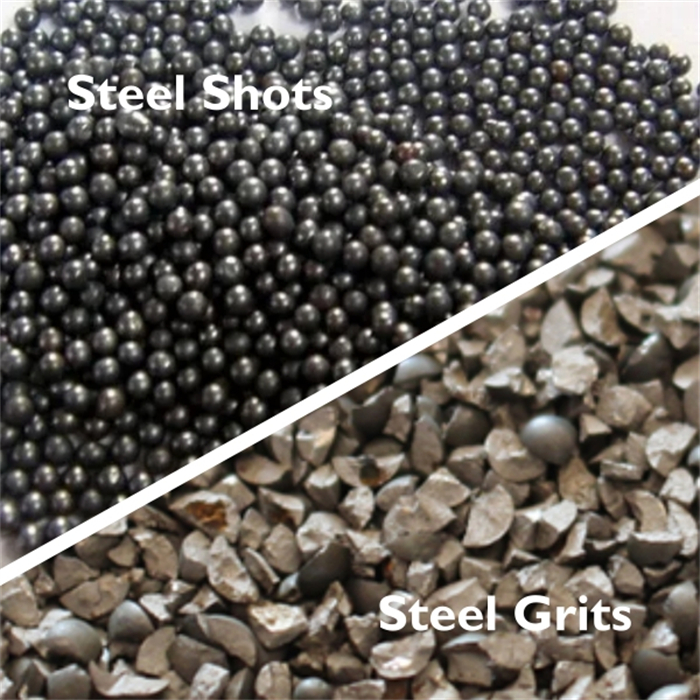
For more aggressive peening or when greater surface hardness is desired, steel grit outperforms steel shot and ceramic beads.
What Are the Benefits of Using Steel Grit for Shot Peening?
Steel grit offers several advantages over other abrasives used in shot peening, particularly in terms of performance and cost-efficiency.
Steel grit provides superior performance in terms of creating consistent compressive stress and prolonging the life of metal components.

One of the primary benefits of using steel grit for shot peening is its high durability. Due to its hardness, steel grit does not break down quickly during the peening process, leading to longer-lasting results. Additionally, its angular shape allows for more aggressive surface impact, which can improve the material’s fatigue resistance and overall longevity. Steel grit is also a cost-effective option because it can be reused multiple times without significant loss of performance, making it a popular choice for industries where efficiency is key.
Steel grit provides an effective, durable, and cost-efficient solution for shot peening, especially in high-volume applications.
What Are the Limitations of Steel Grit in Shot Peening?
Despite its advantages, steel grit may not be the best choice for all shot peening applications. There are certain limitations to consider before choosing it for your project.
The angular nature of steel grit can cause excessive surface damage on delicate components, making it unsuitable for all materials.
One limitation of steel grit is its angular shape, which can sometimes cause excessive surface damage if not used correctly. For more delicate materials, or when a smoother surface finish is required, steel grit might be too aggressive. Additionally, its hardness can make it unsuitable for softer metals, where a gentler abrasive might be more appropriate. In such cases, softer abrasives like ceramic beads or plastic media might be better suited to prevent unwanted surface wear.
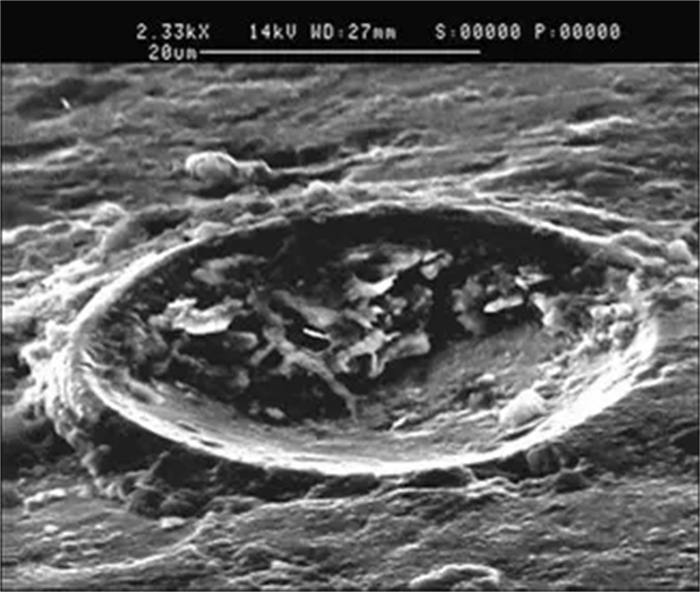
Steel grit may not be the best option for materials that require a more delicate touch or when a smoother surface finish is needed.
Conclusion
Steel grit is a valuable tool in shot peening, providing high durability, consistent compressive stress, and excellent cost efficiency. Its angular shape and hardness make it ideal for improving the fatigue life of metal components, especially in high-impact applications. However, it is important to assess the specific requirements of each project. For delicate materials or where a finer surface finish is needed, other abrasives may be a better fit.