Choosing the right abrasive material is crucial to optimizing the performance and efficiency of abrasive blasting operations. Among the many materials available, steel shots are increasingly the go-to choice for industrial applications. From automotive manufacturing to surface preparation and cleaning, steel shots stand out as a highly effective, durable, and cost-efficient option. But why exactly should you choose steel shots over alternatives such as aluminum oxide, garnet, or glass beads? This article explores why steel shots should be your top choice for abrasive blasting, highlighting their benefits in durability, efficiency, cost-effectiveness, and environmental sustainability.
Steel shots offer numerous advantages over other abrasive materials. With higher durability, reusability, and better performance in various applications, they provide more consistent results, lower operational costs, and a more environmentally friendly solution.
If you’re unsure whether steel shots are the right choice for your blasting needs, continue reading to learn about the significant benefits they offer. By the end of this article, you’ll have a clearer understanding of why steel shots are the superior option for many industries.
Steel shots are the most reliable abrasive material available, offering substantial benefits in terms of performance, cost savings, and sustainability—making them the preferred option in industries worldwide.
We will talk about the following topics in the article
- What Makes Steel Shots Different from Other Abrasive Materials?
- How Steel Shots Enhance Blasting Efficiency?
- What Are Long-Term Economic Benefits of Steel Shots?
- Are Steel Shots a More Sustainable Option?
- Steel Shots vs. Other Abrasive Materials: A Comparative Analysis
What Makes Steel Shots Different from Other Abrasive Materials?
Steel shots are often chosen for their ability to produce precise, high-quality results in abrasive blasting applications. But what sets them apart from other materials, such as aluminum oxide or garnet, that are commonly used for the same purposes?
The primary difference between steel shots and other abrasives is their superior hardness, durability, and spherical shape, all of which contribute to their effectiveness in achieving consistent, high-quality blasting results.
Abrasive Material | Hardness | Tensile Strength (MPa) | Durability | Shape | Typical Applications |
Cast Steel Shots | 40 – 65 HRC | 450 – 550 | High (Reusable) | Spherical | Surface cleaning, rust removal, shot peening |
Fused Aluminum Oxide | 9.0 MOHS | 1,200 – 2,000 | Moderate (Breaks down quickly) | Angular/Irregular | Surface preparation, coating removal, metal cleaning |
Garnet | 7.0 – 8.0 MOHS | 500 – 900 | Moderate (Reusable) | Angular/Irregular | Waterjet cutting, abrasive blasting, surface preparation |
Glass Beads | 5.0 – 6.0 MOHS | 200 – 400 | Low (Breaks easily) | Spherical | Polishing, delicate surface cleaning, peening |
Silicon Carbide | 9.0 MOHS | 1,500 – 2,500 | High (Long-lasting) | Angular/Sharp-edged | Precision cutting, metal surface preparation, grinding |
Steel shots are made from high-carbon steel, which gives them exceptional hardness. Their spherical shape allows for a more uniform impact, which results in even and consistent surface treatment. Unlike irregularly shaped abrasives, such as crushed glass or garnet, steel shots produce a smoother, more consistent finish during blasting. Their uniformity also means they can be reused multiple times, offering a longer lifespan and fewer material replacements.
In contrast, materials like aluminum oxide, although effective for certain applications, tend to break down more quickly. This wear leads to the need for frequent replenishment and higher costs. Steel shots’ resistance to degradation makes them more efficient and cost-effective over time, especially in high-volume operations.
The superior hardness and spherical shape of steel shots, along with their durability, make them the ideal choice for a variety of abrasive blasting applications, ensuring better and more consistent results compared to other materials.
How Steel Shots Enhance Blasting Efficiency?
Blasting efficiency is crucial for businesses that rely on high throughput, such as the automotive, aerospace, and manufacturing industries. So, how do steel shots contribute to improving blasting efficiency?
Steel shots increase blasting efficiency by providing faster cleaning and surface preparation with fewer passes. Their consistent shape and durability reduce the time spent on material replenishment and minimize downtime.
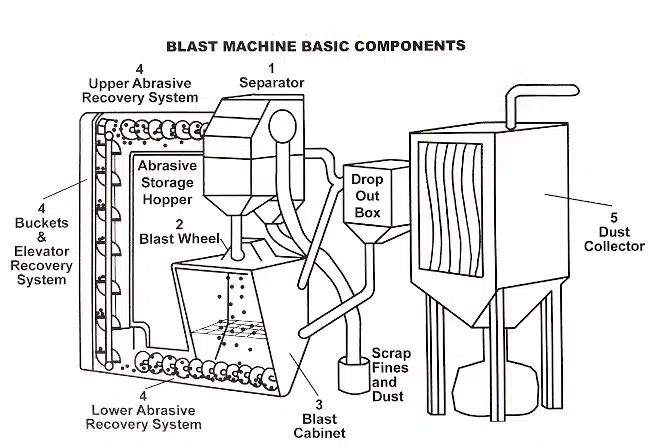
One of the main advantages of steel shots is their ability to maintain their effectiveness through multiple uses. Unlike abrasives that degrade quickly, steel shots are durable and retain their shape, which leads to fewer replacements and reduced operational downtime. Their spherical shape ensures they can cover surfaces evenly and with high precision, requiring fewer passes to achieve the desired finish. This efficiency translates into faster processing times, reducing labor costs and increasing productivity.
In industries where time is money, this ability to streamline operations is invaluable. Whether it’s removing rust from large metal surfaces or preparing components for coating, steel shots make the blasting process more effective and efficient, allowing businesses to meet tight deadlines without sacrificing quality.
Steel shots enhance blasting efficiency by reducing the number of passes required and cutting down on downtime, making them ideal for high-demand environments.
What Are Long-Term Economic Benefits of Steel Shots?
Although the initial investment in steel shots might be higher compared to alternative abrasives, their long-term economic benefits make them the more cost-effective choice in the long run. But how exactly do they contribute to cost savings?
The durability and reusability of steel shots significantly lower operational costs by reducing the frequency of replenishment and waste disposal. Their long lifespan means fewer replacements and less downtime, resulting in overall savings.
Abrasive Material | Cast Steel Shots | Fused Aluminum Oxide | Garnet | Glass Beads | Silicon Carbide |
Reusable | Recyclable | Expendable | Expendable | Expendable | Expendable |
Productivity | High | High | Medium | Low | High |
Initial Cost | Medium | Medium | Low | Low | High |
Equipment | Wheel & Air | Air | Air | Air | Air |
Average Consumption for a SA21/2 Surface Aspect Grade | 0.50kg/m2 | 18.75kg/m2 | 30.00kg/m2 | 30.00kg/m2 | 17.95 kg/m2 |
Average Waste Generation | 0.40kg/ m2 | 15.00kg/m2 | 23.00kg/m2 | 23.00kg/m2 | 29.00kg/m2 |
Applications | Heavy-duty cleaning, peening, and preparing surfaces before coating | Preparing surfaces before coating | Removing contamination | Gentle cleaning | Preparing surfaces before coating |
One of the primary ways that steel shots save money is through their reusability. Because they are highly durable, they can be used multiple times before needing to be replaced. This reduces the amount of abrasive material purchased over time and lowers replenishment costs. Additionally, steel shots have a longer lifespan than many other materials, further reducing operational costs.
Moreover, their durability minimizes waste disposal fees. Many other abrasives break down quickly, requiring frequent replacement and generating more waste. Steel shots, on the other hand, are recyclable and can be reused multiple times, reducing waste disposal needs and contributing to more sustainable practices in the workplace.
Steel shots offer long-term cost savings by reducing material replacement frequency, minimizing downtime, and lowering waste disposal fees, making them an economically sound investment.
Are Steel Shots a More Sustainable Option?
In today’s environmentally conscious world, sustainability is a critical factor in industrial operations. Are steel shots a more environmentally friendly option compared to other abrasive materials?
Steel shots are a sustainable choice because they are fully recyclable and reusable, significantly reducing waste compared to other abrasives that often need to be discarded after use.

Steel shots are made of steel, a material that can be melted down and reused at the end of its lifespan. This recyclability contributes to a lower environmental impact, as the need for new raw materials is reduced. On the other hand, abrasives such as sand, glass beads, and garnet are often single-use and contribute to greater waste and pollution. By choosing steel shots, companies can reduce their environmental footprint while still achieving optimal blasting results.
Furthermore, the durability of steel shots means fewer replacements are required, leading to reduced resource consumption over time. As sustainability becomes a growing concern in manufacturing, using steel shots aligns with best practices in environmental responsibility.
Steel shots offer a more environmentally sustainable option due to their recyclability and reusability, making them a responsible choice for businesses focused on reducing waste and conserving resources.
Steel Shots vs. Other Abrasive Materials: A Comparative Analysis
Now that we’ve covered the advantages of steel shots, how do they stack up against other popular abrasive materials like aluminum oxide, garnet, and glass beads? Let’s take a closer look.
While steel shots are more durable and cost-effective over time, each abrasive material has its strengths and weaknesses depending on the specific application. Understanding these differences can help you make the best choice for your needs.

Aluminum oxide is highly abrasive and can be used for aggressive cleaning and surface preparation. However, it tends to break down faster than steel shots, resulting in more frequent replenishment and higher costs.
Garnet is another popular abrasive, often used for its natural abrasive qualities and lower dust emissions. However, it lacks the reusability and durability of steel shots, making it more costly in the long term.
Glass beads, while gentler and ideal for polishing, do not have the same cutting power as steel shots, which makes them less effective for heavy-duty cleaning or rust removal. While they might be suitable for delicate tasks, steel shots are far superior for more demanding applications, especially when durability and cost efficiency are considered.
Steel shots are the most versatile and cost-effective option for abrasive blasting, outperforming alternatives like aluminum oxide, garnet, and glass beads in both durability and reusability.
Steel shots offer a range of advantages over other abrasive materials, including superior durability, enhanced blasting efficiency, cost savings, and environmental sustainability. Their unique properties make them the ideal choice for a variety of industrial applications, from automotive manufacturing to surface preparation and cleaning. If you’re looking for an abrasive material that delivers consistent results, reduces operational costs, and minimizes waste, steel shots should be at the top of your list.
External Links Recommendations
For more information on steel shots and other abrasive materials, check out the following resources: